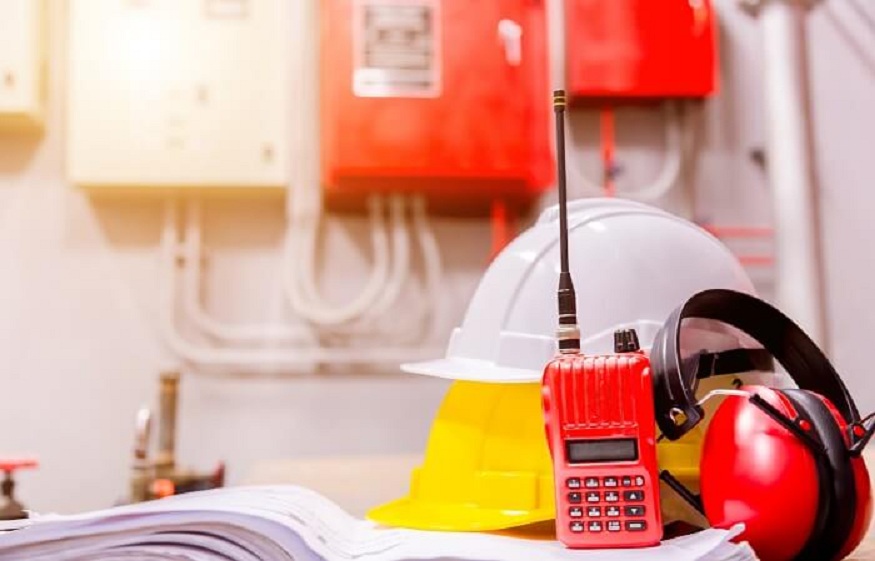
Elements of construction safety management plan
A construction safety plan document details the protocols, guidelines, and laws that have been or will be implemented to safeguard employees during the life of a building project. In addition to laying out responses to safety issues, such as rescue operations, ambulance services, and post-incident evaluation procedures, the document should also emphasise avoiding accidents.
Plans for managing safety.
A construction safety management plan is an evolving document that lists every step that has to be taken to guarantee safety and health at work. This paper is essential to how the Committee on Health and Safety and Management will handle security.
In a construction area, hundreds of incidents may be handled daily, but safety always comes first. Before work begins, it is essential for all employees, including subcontractors—to have a solid grasp of the safety protocols. Without a good WHS management strategy, it is hard to monitor, and you risk facing fines. The complexity of the work environment, including the number of employees present at any moment, and the inherent dangers of the job, will determine the degree of information needed. What do the Work Safety and Health Code of Ethics 2015 say about the components of a WHS management plan?
The essential elements of a safety management strategy
1. A Person
The plan must specify the occupations or functions with particular health and safety obligations. For instance, the list has to include project managers, first aid officers, and WHS managers. It is necessary to outline their duties, and it is not required to designate representatives for health and safety unless they also serve in a coordinating capacity.
2. Consensus-building, collaboration, and coordination mechanisms
The primary contractor must outline in the strategy how everyone involved in a project or company at the workspace will communicate, coordinate, and collaborate. All responsibility holders should constantly speak and work together to minimise risks and hazards by being aware of one another’s building operations when their tasks overlap. People who are in charge of WHS are often absent from the scene. The WHS management program should also contain procedures for consulting with off-site employees.
3. The plans for handling situations
The principal contractor should consider the many safety and health issues that might happen. The plan must include the steps to be followed and the person who will function as the principal contractor’s representative.
4. safety and health laws that are site-specific
Any site-specific WHS regulations mandated by the principal contractor must be included in the safety plan, along with the procedures for ensuring that everyone working there is aware. Rules should be concise and specific about who they apply. The site-specific regulations may be influenced by the kind of work being performed, potential risks, the work’s location and size, and the workforce’s makeup.
Principal contractors can keep track of the necessary communications with a thorough audit trail with a construction management tool.
Additionally, you should make plans to guarantee that the SWMS is rigorously followed by all impacted personnel (including contractors and subcontractors) and that work is stopped if it is not. Although the building safety plan must be created before the start of the project, it needs to be a fluid document that can be easily modified when the project is altered, or new dangers are found on the work site.